I tried a new product from Rio Grande called imbedables (new to me) and really like it, so thought I would share. These are fusible bails! This was a test, so they are not perfect, but now I know what to do differently the next time around.
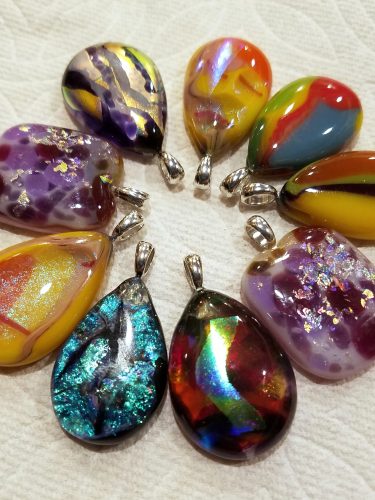
1 – I made cabochons in a mold, making them a bit on the thick side. (Some of them I used some old “pebbles” in the mold and added dichro). After taking out of the mold, I cleaned them up by grinding as needed and cleaning really well.

2 – using my ring saw I sliced into the tip of the glass, just deep enough for the full length of the bail. The square pieces I drilled with a dremel, but didn’t like the effort it took and the outcome – maybe a drill press would make it easier.

3 – Insert the bail using a dab of glue taking care to center and straighten the bail. Don’t do as I did and forget these are SILVER – which requires a dedicated shelf (oops).
4 – Fuse to close up the slice (or drilled hole) and fire polish. Next time I will go a few degrees hotter and hold a couple minutes longer as these didn’t quite fully close (close enough for a test). Maybe even add a few bits of frit on the sides of the cut.
5 – They will come out ugly, looking like a galvanized nail, but that is easily dealt with by 24 hours in a rock tumbler.
